Vault best practices
The Perks of Automated Publishing
How to knock off file publishing from your list and increase your drawing output by 25%
PDF files have long been a standard format for industrial applications, in particular PDF/A and PDF/E have become standardized for use in engineering workflows and long-term document storage. [1] For this reason, PDFs are a crucial part of the design engineering process.
To find out how crucial, we recently conducted a survey of our customers.
We asked more than 250 of our customers how many PDFs they generate per month, per designer.
The answer was between 150 and 200.
PDFs are created when a new drawing is needed, or a modification is required to an existing drawing, and these drawings typically result in manufacturing output. As such, the rate of drawing, and PDF, production is the currency for measuring design efficiency.
One of the products we provide to our customers, powerJobs, integrates with Autodesk Inventor and Vault to automate production of PDF, DXF and STEP files, so in follow up to the first question, we asked about the productivity gains of publishing automation.
We discovered companies that were using powerJobs to automate the generation of these files were able to increase design throughput significantly, on average, by 25%.
Looking at that another way, that’s equivalent to adding an additional designer to an existing team of four, or by increasing the average working day from eight to ten hours.
[ ON-DEMAND ONLINE WEBINAR ]
Everything you need to know about process Automation
- How to increase your design thoughput
- How to improve file quality process efficieny
- The highlights of powerJobs
- Easy customization options
- Some of the main use cases
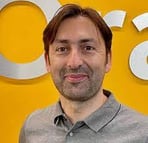
Marco Mirandola
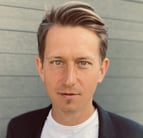
Christian Gessner
Efficiency gains are one positive aspect of publishing automation, but our customers tell us that another important factor is how much time, and therefore, cost is saved through automation compared to the manual creation of PDFs, DXFs and STEP files.
Reducing the amount of time it takes to create those files can result in considerable savings. By way of illustration, we can look at the quantitative gain for the team and the company through a simple mathematical exercise. We can determine the cost of the time saved through the use of automation as:

Where:
Davg = average number of drawings touched by each designer per day
N = number of designers
t avg = average time to create a PDF
Wavg = average number of working days per month
C = average gross hourly cost of a designer
For this exercise, let’s assume a team of 5 designers creates/modifies 4 drawings a day, each of which takes 90 seconds to generate and store the PDF in the appropriate location, with the correct naming convention. We can further assume an average gross hourly designer cost of €70 per hour, therefore:
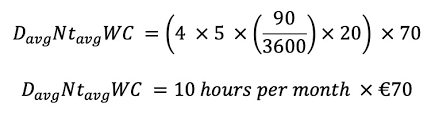
quantitative cost benefit of PDF automation
= €700 per month
= €8400 per year
= €2400 per designer per year
The cost is one thing, but also consider that this represents 2 ½ hours a month where valuable, highly qualified designers are occupied with menial admin tasks.
Take the test now and determine the cost of the time saved through the use of automation
With a 25% increase in throughput, and an associated cost benefit of €2400 per designer per year, it leads to the question of why so many companies are still doing this manually?
This isn’t just an opportunity for small design teams like the illustration above, but also for larger companies with much larger teams. However, in our experience, we find that small companies with perhaps just two or three Inventor or Vault seats are often much more likely to see the return on investment (ROI) of publishing automation than larger companies.
Perhaps smaller companies are simply under pressure to deliver more with less and are thus looking for cost-effective ways to increase productivity, whilst also freeing up more time to be spent on higher-value, more intensive tasks.
Besides the quantitative gain, there is also a huge qualitative gain. What happens if the PDFs are not updated or created, or they are completed too late? Delays in the production of documents have knock-on effects through the whole production chain. Delayed, incomplete or missing documents can result in unplanned production costs for incorrectly manufactured or ordered parts, and delays in the assembly line, which can impact delivery dates, and lead to further financial costs, project details or even contractual penalties.
Beyond the quantitative and qualitative improvements that production automation can bring, there is one other benefit I’d like to mention. Reduced distraction.
Communication between different teams is often a good thing and should, generally, be encouraged for healthy companies. However, some interactions are purely distractions that slow down other tasks. One example of this is when a team member feels the need to check with the designer “just to be sure” that the PDF, DXF, STEP file they are using is really the latest and greatest version.
Lack of certainty like this can multiply across an organization, and lead to a noticeable level of interruption and distraction for the designers. By automating the process of publishing drawings (PDF) and models (DXF, STEP), everyone outside the design team knows they can trust the data and work more autonomously, thereby reducing time-wasting distractions and interruptions that affect concentration and delivery.
How To Increase Design Engineering Efficiency
Whether your design team has just a few seats or several hundred, automating the publishing of PDFs, DXFs, STEPs (and perhaps more) increases efficiency within the design department, reduces production waste and assembly line delays, contributes to time-to-market, and builds trust within the company by reducing unnecessary “double checks”. If you’re still doing these types of tasks manually, it’s time to make technology work for you and make a small investment to knock this issue off your list.
powerJobs is the best-in-class Vault Job processor extension for Autodesk Vault customers, that provides ready-to-use jobs for publishing, as well easy customisation options to meet unique customer requirements.
Get in touch with us today to find out more about powerJobs.
[1] https://www.iso.org/obp/ui/#iso:std:iso:19005:-3:ed-1:v1:en, https://www.iso.org/standard/42274.html
At COOLORANGE, we have the expertise, tools and a proven track record to help you on your automation journey. Established 12 years ago, COOLORANGE has decades of experience working with engineering and design organisations using Autodesk tools. Our experienced engineers and accredited Autodesk reseller partners are on hand to help identify and implement the automation you need to enhance your engineering operations and deliverables, and make the most of the Digital Transformation, process automation opportunity.